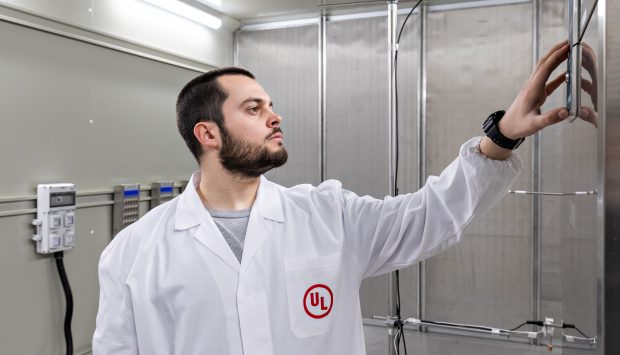
I gas Fluorurati se ne vanno, ma arriva il pericolo di incendi…
Nils Meinhardt, Global Business Development Manager HVAC, UL
Entro il 2025, ai produttori del settore del condizionamento dell’aria e della refrigerazione, sarà consentito utilizzare solo refrigeranti con un basso potenziale di riscaldamento globale. Tuttavia, molti dei gas ammessi, sono infiammabili e per la prima volta richiedono un’analisi del rischio precisa e possibilmente test pratici.
Il tempo sta scadendo, entro il 2021, le emissioni di gas fluorurati (gas F) dovranno essere dimezzate rispetto al 2015, e ridotte di circa l’80% entro il 2030. Verrà applicata una riduzione graduale, anche se questa impatterà i diversi tipi di attrezzature in modo differente. Già nel 2020, i sistemi di refrigerazione commerciali sigillati ermeticamente possono essere venduti solo se il gas utilizzato ha un potenziale di riscaldamento globale inferiore a 150, e quasi tutti i gas conosciuti al di sotto di questo valore sono infiammabili.
Non tutti i costruttori hanno già preso delle misure rispetto a questo importante cambiamento. I sistemi di refrigerazione commerciali, ma anche i sistemi per il condizionamento dell’aria e le pompe di calore devono essere rapidamente convertiti per poter essere venduti sul mercato in futuro. Benché i fluorocarburi (HFCs/HFCs) comunemente utilizzati fino ad ora, non danneggino lo strato di ozono nell’atmosfera, sono dei gas nocivi per il clima e la loro diffusione contribuisce al riscaldamento globale in modo significativo. L’ industria deve pertanto passare a refrigeranti con un potenziale di riscaldamento globale relativo (GWP) di gran lunga più basso.
I refrigeranti naturali come CO2, isobutano, propano o ammoniaca, insieme ad alcuni HFO, permettono di stare sotto il limite di 150 Global Warming Potential GWP. Per confronto, il valore di GWP di R-134A è di 1430, cioè quasi dieci volte più alto del potenziale di riscaldamento globale dei refrigeranti naturali. Tuttavia, i gas che meno danneggiano il clima pongono nuovi problemi perché, con l’eccezione della CO2, sono infiammabili o tossici. Per questo, sono necessarie maggiori precauzioni di sicurezza sui dispositivi.
Il rischio di incendio legato ai refrigeranti infiammabili è una caratteristica di prodotto decisiva per cui, contrariamente al passato, è necessario richiedere un’analisi dettagliata dei rischi secondo i requisiti di prodotto. Per dirla in modo semplice, fino ad ora i produttori hanno solo determinato che le attrezzature fossero sicure in termini di rischio di incendio ma questo approccio non è più sufficiente perché per i nuovi refrigeranti come R454C, R1234yf o il propano, ricadendo come minimo nella classe di infiammabilità 2L, è necessaria un’estesa analisi di rischio sia dei dispositivi sia degli impianti.
Valutazione dei rischi ai sensi della legge UE
La valutazione dei rischi è regolata dalla Direttiva ATEX. Richiede un esteso processo di valutazione dei rischi che comprende tutti i componenti di un dispositivo, tutti gli scenari applicativi e tutti i pericoli noti. Il produttore deve dunque decidere se esiste un rischio accettabile o se sono necessarie delle misure aggiuntive per ridurre il rischio. Questo processo include, tra gli altri, i seguenti punti:
- Definizione dell’uso voluto e dei limiti di utilizzo
- Riconoscimento delle interazioni tra componenti e processi all’interno dei dispositivi
- Rilevazione di potenziali fonti di accensione
- Riconoscimento delle interazioni tra componenti e sostanze nei dispositivi
- Determinazione della probabilità dei pericoli rilevati
- Stima della gravità del danno potenziale
- Determinazione dei rischi residui
Informazione agli utenti in merito a tutti i pericoli
Una misura importante per la riduzione del rischio è che non si crei un’atmosfera esplosiva all’interno del dispositivo o nelle sue immediate vicinanze. Molti costruttori dovranno dunque riprogettare completamente le loro attrezzature e i loro sistemi: infatti, poiché fino ad ora hanno utilizzato solo refrigeranti non-infiammabili, i componenti elettrici sono spesso posizionati in alloggiamenti che potrebbero far sorgere improvvisamente fonti di ignizione. Per esempio, i relè e gli interruttori adesso dovranno essere schermati o installati in un alloggiamento separato. Un’altra possibile misura di sicurezza è l’utilizzo di un dispositivo che spenga stati pericolosi, per esempio interrompendo l’alimentazione, o l’installazione una ventola per disperdere più velocemente gli eventuali gas in fuoriuscita.
Questi esempi fanno già capire che sarà necessario ripensare la progettazione di molti dispositivi. Inoltre, costruttori e utilizzatori devono considerare i passaggi rilevanti della “Hazardous Substances, Workplace and Operational Safety Ordinance” (Ordinanza sulle sostanze pericolose, sul posto di lavoro e la sicurezza operativa). Ad esempio, il sito operativo dell’impianto deve essere adeguatamente ventilato e quando si lavora al suo interno, potranno essere utilizzati solo strumenti appositi. Inoltre, la quantità di riempimento del refrigerante dovrà essere adattata alla dimensione della stanza, in questo modo si evitala formazione di una miscela di aria combustibile/refrigerante.
Le simulazioni a computer completano i test fisici
In breve: un’analisi dei rischi nella tecnologia del condizionamento dell’aria e della refrigerazione non può essere implementata velocemente. Affermazioni valide sui rischi e sulla probabilità che si verifichino possono essere ottenute solo attraverso test fisici dettagliati, ma sono molto costosi e dispendiosi in termini di tempo. Per questo motivo, la maggior parte dei produttori sceglierà di non eseguire tutti i test immaginabili ma di limitarsi a certi rischi plausibili. Tuttavia, in singoli casi questo può significare un rischio residuo troppo grande.
In ogni caso, esiste un utile supplemento ai test fisici: una simulazione al computer. Può essere utilizzata, ad esempio, per controllare tutti i tipi di perdita da un’unità di refrigerazione o di condizionamento dell’aria. Alcuni dei parametri decisivi sono il posizionamento ed il tasso di perdita di gas e la posizione della fonte di accensione. Contrariamente ad un test fisico, in una simulazione al computer, questi parametri possono essere modificati a piacere, così come possono essere modificate condizioni ambientali quali la temperatura della stanza o le correnti d’aria da un sistema di ventilazione.
Nel modello di simulazione, ognuno di questi parametri può essere impostato, in questo modo, la perdita e la fonte di accensione potranno essere posizionate liberamente per valutare l’effetto di una perdita di gas. Questo non sarebbe possibile in un test reale per ragioni di tempo e costo. Un ulteriore vantaggio della simulazione è il breve tempo di consegna di una singola simulazione, che può essere di appena alcuni secondi. In questo modo, è possibile calcolare e confrontare un’enorme quantità di dati in un tempo molto breve.
Al termine di una serie di simulazioni, c’è una comparazione di tutti gli scenari che devono essere considerati, il che consente al produttore di valutare il rischio più basso. Se l’affidabilità dei risultati trovati è ancora troppo alta per via della qualità del modello o dei dati forniti, i risultati possono essere confermati da un test fisico reale.
Solo modelli di simulazione validati sono utili
Una simulazione è buona se lo sono i dati forniti al modello: il modello utilizzato deve essere valido e riprodurre in modo preciso i risultati di un corrispondente test empirico. Questa non è una banalità: UL ha sviluppato un proprio modello di simulazione per l’analisi dei rischi nella refrigerazione e lo ha testato a fronte di test fisici. Varie combinazioni di perdite di gas refrigeranti e fonti di accensione disposte in modi diversi sono state simulate in un’impostazione di test definita.
Questa impostazione di test è stata poi simulata nella realtà e testata. In questo caso la simulazione deve essere intesa come una prognosi ed il test pratico come la verifica empirica. Se il flusso previsto e il comportamento di incendio non si verificano, il modello di simulazione viene rivisto e testato di nuovo empiricamente. Questa validazione del modello richiede molto tempo ma semplifica l’utilizzo nelle quotidiane operazioni di test. Simulazioni al computer valide sono un modo eccellente per confermare una valutazione dei rischi secondo la direttiva ATEX.
Il tempo è fondamentale per i produttori così come per gli importatori e i costruttori di impianti nei settori della refrigerazione e del condizionamento dell’aria. E dato che la UE li ha obbligati a dar prova delle certificazioni e delle analisi dei rischi corrispondenti, queste simulazioni al computer aiutano ad utilizzare il tempo in modo efficiente fino al 2020 e oltre a seconda dell’applicazione, ed a convertire l’intera gamma di prodotti in refrigeranti con bassi GWP.