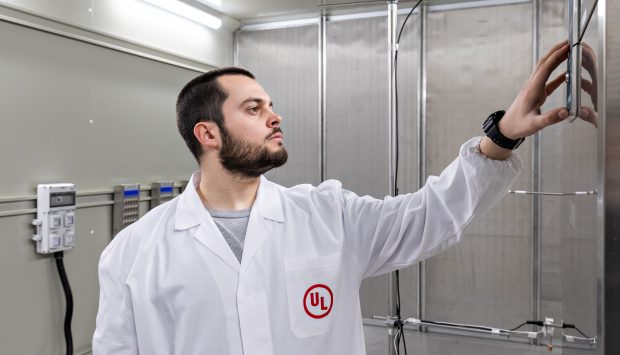
F-gases go, the fire danger comes
Nils Meinhardt, Global Business Development Manager HVAC, UL
By 2025 at the latest, manufacturers will only be allowed to use refrigerants with a low global warming potential in air conditioning and refrigeration technology. However, many of these gases are flammable and for the first time require a precise risk analysis and possibly practical tests.
The clock is ticking. By 2021, emissions of fluorinated gases (F-gases) must be halved compared with 2015 and reduced by approx. 80% by 2030. A step-by-step reduction will apply, although this will affect individual types of equipment differently. As early as 2020, hermetically sealed commercial refrigeration systems may only be sold if the gas used has a global warming potential of less than 150. Almost all known gases below this value are flammable.
By far not all manufacturers have reacted yet. Commercial refrigeration appliances but also air conditioning systems and heat pumps must be quickly converted in order to be able to sell successfully on the market in the future. Although the fluorocarbons (HFCs/HFCs) commonly used to date do not damage the ozone layer in the atmosphere, these are climate-damaging gases whose spread contributes significantly to global warming. Industry must therefore switch to refrigerants with a lower relative global warming potential (GWP).
Natural refrigerants such as CO2, isobutane, propane or ammonia together with some HFOs can undercut the 150 GWP limit. By comparison, the value of R-134A GWP is 1430 – almost ten times the global warming potential of natural refrigerants. However, the less climate-damaging gases pose new problems because, with the exception of CO2, they are flammable or toxic. For example, additional safety precautions are required on the devices.
The risk of fire from flammable refrigerants is a decisive product feature for which a detailed risk analysis is required according to European product requirements – unlike in the past. To put it somewhat simply, manufacturers have so far only determined that the equipment is harmless in terms of fire hazard. This is no longer sufficient because the new refrigerants such as R454C, R1234yf or propane are at least classified in flammability class 2L. Therefore, a comprehensive risk analysis of the devices and plants is necessary.
Risk assessments under EU law
Risk assessment is regulated in the ATEX Directive. It requires a comprehensive hazard assessment process that includes all components of a device, all application scenarios and all known hazards. The manufacturer must then decide whether an acceptable risk exists or whether additional measures are necessary to reduce the risk. This process includes the following points, among others:
- Defining the intended use and the limits of use
- Recognition of interactions between components and processes within the devices
- Detection of potential ignition sources
- Recognition of interactions between components and substances in the devices
- Determining the probability of detected hazards
- Estimate the severity of potential damage
- Determination of residual risks
- Creating user information that informs about all hazards
An important risk reduction measure: An explosive atmosphere must not be created inside the device or in its immediate vicinity. Many manufacturers will therefore have to completely redesign their equipment and systems. As they have so far only used non-flammable refrigerants, the electrical components are often placed in a housing in such a way that ignition sources could suddenly arise. For example, relays and switches must be shielded or installed in a separate housing. Another possible measure is a device for switching off dangerous states, for example by interrupting the power supply. It also makes sense to install a fan to distribute escaping gases more quickly.
These brief remarks already show that the design of many devices must be rethought. In addition, manufacturers and users must also consider the relevant passages of the Hazardous Substances, Workplace and Operational Safety Ordinance. The operating site of the plant must be adequately ventilated, and only suitable tools may be used when working on it. In addition, the filling quantity of the refrigerant must be adapted to the size of the room. This prevents the formation of a combustible air/refrigerant mixture in the worst case.
Computer simulations supplement physical tests
In short: a risk analysis in air conditioning and refrigeration technology cannot be implemented in passing. Valid statements on risks and their probability of occurrence can only be obtained through detailed physical tests. But they are very costly and time-consuming. For this reason, most manufacturers will switch to not carrying out all conceivable tests but limiting themselves to certain plausible risks. In individual cases, however, this can mean too great a residual risk.
However, there is a useful addition to physical tests: a computer simulation. It can be used, for example, to check all types of leakage from a refrigeration or air conditioning unit. Decisive parameters include the location and rate of gas leakage and the position of the ignition source. In contrast to a physical test, these parameters can be varied at will. In a computer simulation, environmental conditions such as room temperature or draughts can also be varied at will by a ventilation system.
In the simulation model, any number of data points can be set for each of these parameters. In this way, leakage and ignition source can be freely positioned elsewhere in small steps in order to evaluate the effect of a gas leak. This would not be possible in a real test for reasons of time and cost. A further advantage of the simulation is the short lead time of a single simulation, which may be only a few seconds. In this way an enormous amount of data can be calculated and compared in a very short time.
At the end of a series of simulations there is a comparison of all scenarios to be considered, which allows the manufacturer to evaluate the lowest risk. If the reliability of the results found is still too high due to the quality of the model or the data provided, the results can be confirmed in a real physical test.
Only validated simulation models are helpful
A simulation is only as good as the data provided to the model: The model used must be valid and precisely produce the results of a corresponding practical test. This is not a trivial requirement. UL has developed its own simulation model for risk analysis in refrigeration and tested it against physical tests. Various refrigerant gases with differently arranged leakages and ignition sources were simulated in a defined test setup.
This test setup, including the gas leaks and ignition sources, was then simulated in reality and tested in practice. Here the simulation is to be understood as a prognosis and the practical test as the empirical verification. If the predicted flow and fire behaviour does not occur, the simulation model is revised and empirically tested again. This validation of the model is very time-consuming but simplifies the use in everyday test operation significantly. Valid computer simulations are an excellent way to confirm a risk assessment according to the ATEX directive.
Time is of the essence for manufacturers, but also for importers and plant manufacturers in the field of air conditioning and refrigeration technology. Because the EU has given them the obligation to prove the corresponding certifications and risk analyses. Computer simulations help to effectively use the time until 2020 and beyond, depending on the application, and to convert the entire product range to refrigerants with low GWPs.
This article was originally published in Household Appliance (HA) Factory, to read the full article visit this link.